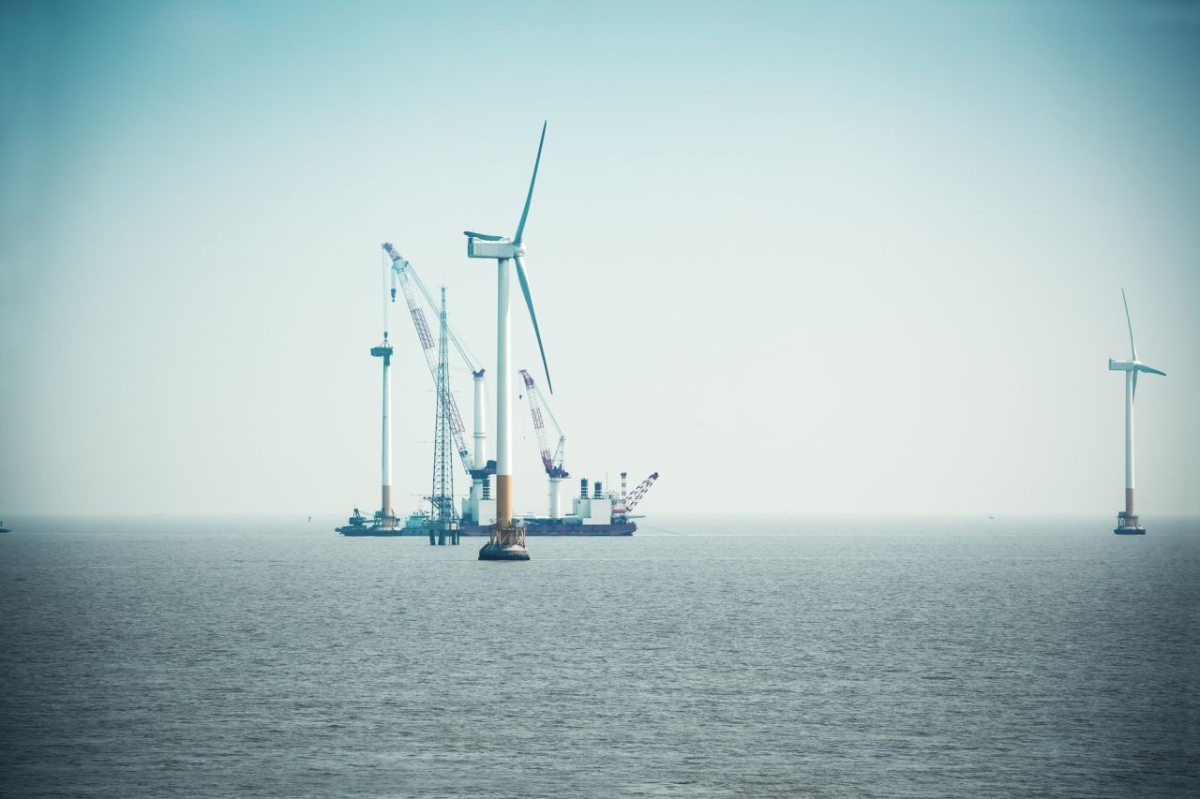
We hear about newer and newer solutions for offshore. How do
technological innovations affect the sector today?
First,
we have IT systems. Marine turbines are fundamentally different from
those we have on land. At sea, their service availability is not so
obvious, we are dependent not only on the distance of 30-40 km from
the shoreline, but also on the weather. So it is known that these
complex power systems,as we call them, work without direct operator
supervision and must be remotely controlled. They work continuously,
because the offshore turbine has to work at least 330 days a year for
25 years. Correct operation of wind turbines – i.e. with the
highest efficiency and maximum power – requires the use of complex
IT systems. Today we are talking about capacities of 14-15 MW.
Translating this into the dimensions and weight of the wind turbine,
we have a rotor diameter of 220-240 meters. The rotor with a drive
unit weighing several hundred tons is seated at a height of up to 150
meters. And it's all spinning.
One issue is the IT system,
which is to support people in the field of everyday use, and another
one – diagnostic and service supervision. Working turbines must be
periodically inspected and diagnosed. Here, artificial intelligence
and robotics are used. I had the opportunity to visit the
construction of a wind farm in Saint-Nazaire. I saw how such a system
is being prepared and talked to representatives of companies that are
involved in the construction of offshore wind farms in France.
And
what did you find out there?
I had the opportunity to observe a lot of
technological innovations, such as the possibility of assessing the
technical condition of wind turbines with the use of drones
adequately equipped with measuring equipment.
They also use
robots to assess the technical condition of rotor blades. The latest
British product is the Blade Bug inspection robot. It is able to move
on a 100-meter rotor blade, registering the condition of its surface.
It has special suction cups, similar to those used for ECG testing.
It is a very complicated device. Interestingly, the founder,
originator, and head of this company has Polish origins.
Which
country appears to be the most technologically advanced for
offshore?
Denmark has a monopoly in IT systems. About 20
years ago, Vestas patented SCADA (Supervisory Control and Data
Aquisition). It is a unified system for monitoring the
operation of wind turbines. It collects measurement data, visualizes
data on computer screens and supports the control of the energy
process. It consists of: switching on, switching off from traffic,
load change, alarming, archiving and reporting of data. You can
connect to this system from anywhere in the world, as long as you
have access to the Internet.
SCADA is a system that was
created 20 years ago?
Yes. It is unified and constantly
improved. Most wind farms, not only offshore but also onshore, use
this system, with the possible exception of China. The number of
control parameters that this system monitors online is in the order
of 30-50 and more.
There are also electroacoustic systems
(SODAR, Sound Detection and Ranging) and electrooptics (LIDAR, Light
Detection and Ranging). The first uses the frequency variation of the
reflected audio signal. In this way, we are able to very precisely
estimate the speed and direction of the wind. The second measures it
in the same way with a laser beam.
How do these electro-optical systems work?
At sea, we
have air with a certain humidity. In fact, it is dry air with water
droplets, and most often salt is dissolved in them. We have a cloud
that is not visible to the naked eye, but in an acoustic or laser
image – it is. The use of optoelectronics is a new thing, it is a
definite step forward when it comes to monitoring and control
systems.
The basic parameter is wind speed. We have to adjust
the angular velocity of the rotor's rotation to it. This is called
speed ratio, which characterizes the speed of rotation of the blade
tip in relation to the wind speed. We achieve the maximum power from
the wind stream when this ratio is optimal. This, of course, has to
be done by the automaton, especially at sea.
What are the
other offshore challenges in which a robot can do the
job?
Interesting challenges for offshore wind farm operators
are related to carrying out maintenance. If something happens to the
onshore turbine, the service team goes and gets to the nacelle
upstairs. Sometimes it may be enough to enter the control system in
the tower's base segment - the first one which goes above the foundation.
It
must be more difficult at sea.
Replacing components in marine
conditions is extremely complicated. We still have to take into
account the dimensions and masses placed at heights (300-500 tons
installed at a height of nearly 150 m). It all has to work without
direct supervision.
At sea, wind turbines are at least three
times larger in terms of generated power. The systems are more
complex. On land, you can go, see what is happening, shut down the
turbine wheel if necessary, and repair it. Such a prosaic matter -
the use of sea turbines in winter conditions. At sea, in cold
weather, there is a high probability of the rotating blades icing up,
which translates into vibration. And if excessive vibrations occur,
such a structure will sooner or later break, according to Wöhler's
law. To prevent this, the blade heating system is activated - a
signal from the sensor initiates the activation of hot air. It's a
mechanical way. It can also be like in cars, where the heating coil
is turned on on the rear windows. Example: the control system catches
vibrations that show that we are dealing with the loss of stability
of the mechanical system of the turbine rotor, e.g. due to material
losses or deformation of the blades. Sea weather conditions do not
always allow access to the property.
How is it
organized?
Through two networks - Ethernet and Internet.
Dozens of parameters that are observed characterize not only the
operating condition of the turbine, but also the vibration condition
of the entire structure. All of this is measured online. This is what
the SCAIME control and measurement system is used for. It collects
data from optoelectronic sensors embedded in the structural structure
of blades, towers or foundations already at the stage of their
production. Here, too, there is a problem with the availability of
such a system and its repair in the case of an offshore turbine. A
separate metrological problem is to ensure the measurement
reliability of the optoelectronic converters used throughout the
turbine's "life" cycle, ie for 25 years.
Of course,
an offshore wind farm usually consists of nearly 30-70 turbines. The
core of the farm is a substation to which the electricity generated
in individual turbines is sent. It is properly processed there and as
direct current it is sent via a submarine cable 30-40 km ashore to
the shore station. Through this cable, in addition to the fact that
there are electric wires in it, a fiber optic bundle is drawn,
through which the measurement data is sent to the land station.
Parameters must be processed and then submitted to diagnostic
conclusions.
How is this information properly handled?
This
is where AI (artificial intelligence) comes in - neural networks,
expert systems that support the operator's decisions. Because at the
end of this chain is the operator who operates the land-based
diagnostic center. A whole team of people work there to check whether
the use can be continued or if some regulation needs to be made.
Worse if there is something wrong with the turbine. This can apply to
any, even the most perfect technical object.
Can systems that
inspect turbines eliminate human workforce?
Yes. They even have to! The
basic activity of a diagnostician is examining the object by means of
measurements. Then he carries out diagnostic conclusions and makes a
diagnosis. Here, all these activities, starting with measurement,
must be supported by the work of IT systems. The process of
monitoring offshore wind turbines is almost entirely carried out by
automatic and robotic devices. On the other hand, the decision to
turn off the turbine when its control parameters do not exceed the
threshold values is up to the human (operator).
What about servicing? Can automation also replace humans
here?
Not that far. We automatically service turbines at
the online condition assessment stage. It is not possible to perform
repairs on a remote system.
I watched the Blade Bug robot in
action, which replaces these characteristic figures of service
technicians hanging on the ropes attached to the turbine blades that
we see on the Internet. People go inside the shovel and check if
something has broken. So it goes towards replacing humans with
robots. The drone can also record and analyze optical and acoustic
signals.
The fact that the team will go "to the turbine"
should be a last resort. As I said, the weather can change rapidly at
sea. Service crew can get there, but have trouble getting back. I
know this from a message from an engineer friend who worked on
offshore wind farms and mining platforms in the USA. In order to work
on servicing the turbine, you must have the appropriate
psychophysical features. And the Baltic Sea is not a pleasant sea,
especially in the transitional seasons of autumn, winter and
spring.
So it is better to prevent than to cure - that is, in
this case, to service?
Be one step ahead of the moment when damage occurs.
Take the turbine out of service before secondary damage occurs. For
example, even the best-made bearing that is subjected to variable and
excessive loads may fail. It is only a small element of a very
complex mechanical system, but its damage, which we define as primary
in diagnostics, may cause secondary damage to the entire drive unit,
including the breakage of the rotor blade, breakage of the
transmission shaft or reduction gear. This causes a huge scope of
work on restoring the technical condition. It is complicated on land,
too, but not quite like at sea.
How quickly could drones or
robots like Blade Bug be spread?
When I was in St. Nazaire,
not only offshore turbine giants, such as GE, Vestas or Siemens
Gamesa, were present there, but also smaller companies specializing
in technological innovations. Blade Bug was to be put into operation
as early as 2022. Its possibilities are huge. We are talking about
equipping robots and drones with appropriate measuring equipment. The
basis here is the SCADA system - collecting parameters, their
processing and inference. This should go hand in hand with the
construction of offshore wind farms. However, the availability of
information about innovations in this respect is not common. The
information provided on the Internet is only rudimentary.
What
is the future for offshore wind turbines? Will they be placed bigger
and bigger or maybe more and more extended - that is,
floating?
Floating wind farms are undoubtedly the future.
Admittedly, these will also be bigger and bigger. If we have stronger
winds at sea, we can build larger turbines. The larger the turbines,
the greater the technical and technological challenges. However, as
we are already betting, if the construction cost (at the investment
stage it is estimated at 1.5-2 million EUR for 1 MW of power)
returns, it is better to put the largest turbines at sea. However,
this must be followed by ever larger ships and installation devices
for building turbines at sea - jack-ups, cranes, etc. Vessels for
erecting the largest turbines are available in a limited number. So
there are additional investment costs. On the other hand, the world's
leading centers, we also at the Gdańsk University of Technology, are
currently conducting research into floating wind farms. Even if
placed in the middle of the ocean, they will be able to generate and
send electricity to land. Maybe it is an illusory vision today, but
tomorrow it will be everyday life. Research work is moving in this
direction.
I understand that in the case of "floats"
inspection systems will be even more important, because servicing
will be even more difficult?
Exactly. There is one more point.
Research and development work is also aimed at recovering excess
energy from the wind. This was the case recently when we heard from
the media that the British had a problem because the wind was so
strong that they didn't know what to do with it. It also happens that
we have excess electricity from the wind. Therefore, the issue of its
processing and accumulation in the so-called cogeneration systems of
various types of energy. Here it is envisaged that the wind turbine
will cooperate with an electrolyser that would produce hydrogen.
This, in turn, would be used for the secondary production of
electricity in a fuel cell, e.g. to power service ships. There are
also pressure accumulators in which electricity is used to compress
the air and store it in underwater pressurized warehouses. Later,
when there is no wind, it could drive the air turbine along with the
generator for the secondary production of electricity. Therefore,
energy storage is a very important challenge. At the same time, hydrogen technologies
are being developed.
Are the innovations in offshore winds implemented faster
than in other industries?
Today, technological research is practically
not carried out without the participation of industry. In order to obtain a
grant, universities cooperate with an industrial
partner, the latter most often being the leading unit. Being in
France at the Seanergy conference, I established many contacts with
scientists and visited university stands. The stands of the
University and the Polytechnic University of Nantes were crowded. I
had difficulties in talking to a certain professor, because so many people
in the industry seek specialist offshore consultations from French
scientists. We in Poland do not have it yet, because we do not have
working turbines in the Baltic Sea. It will be different when this
technology finally reaches us and becomes more tangible.
Does
it mean that Polish science will also benefit from offshore wind
farms?
I hope so. The worst-case scenario would be if, for
example, Danes, Germans or Americans would come, set up offshore wind
farms, train 50-100 people in their operation and leave. After all,
operational problems will always arise. As for the development of new
production technologies, our possibilities are more limited, but at
the operational stage there is hope that the owners of wind farms
will use the help of Polish universities, at least in terms of
specialist consultations, and maybe also commissioned scientific
research.
Prof. dr hab. Eng. Zbigniew Korczewski - lecturer at the Gdańsk University of Technology at the Institute of Ocean Engineering and Ship Technology, Department of Marine Power Plants. Author of many publications, including: Operational diagnostics of marine piston and turbine internal combustion engines, Endoscopy of marine engines and Methodology of testing marine fuels in real operating conditions of a compression-ignition engine.